Automatyzacja produkcji – jak zapobiegać reklamacjom i poprawić jakość wyrobu
Robert Maciągowski
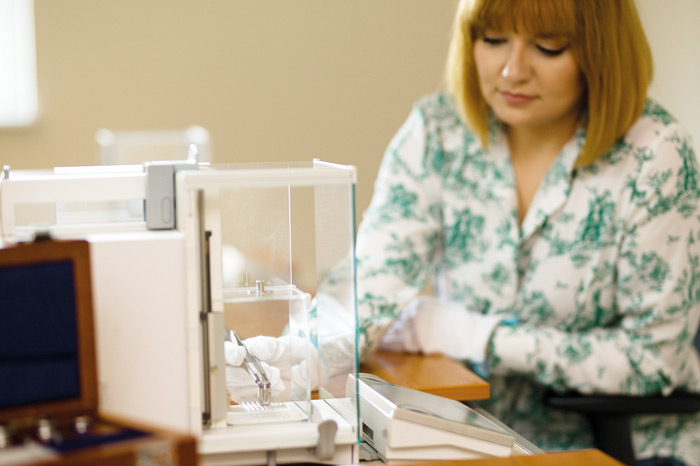
Nieodłącznym elementem realizacji działalności w przemyśle, a przede wszystkim w zakładach produkcyjnych, są narzędzia pomiarowe.
Jakość produkcji to pierwszy element wymagany przez każdego klienta, razem z adekwatnością jakości do ceny. Pierwotnym i podstawowym sposobem jej weryfikacji jest ocena zgodności gotowego wyrobu ze specyfikacją dostarczoną przez Zamawiającego. Zachowanie odpowiednich proporcji, wykorzystanie konkretnych procesów technologicznych, wygląd, funkcjonalność, cechy wizualne i fizyczne muszą zgadzać się z założonymi, inaczej wyrób określa się jako wybrakowany. Obecnie formą zapobiegania, a także kontroli wyrobów końcowych są systemy jakości określające procedury, jakich przedsiębiorstwo musi się podjąć, aby spełnić owe wymagania. Wszelkie błędy i uchybienia w procesie produkcji są możliwe, bowiem ani człowiek nie jest nieomylny, ani maszyny nie są stuprocentowo niezawodne. Lata rozwoju w zakresie usprawniania procesów produkcyjnych ukazały jednak, iż wielu niedociągnięciom można zapobiec i skutecznie zniwelować znaczne straty finansowe. Wdrażanie korzystnych zmian w procesach, kadrach, organizacji, maszynach czy dostawcach musi jednak dojść do skutku jeszcze przed podjęciem zamówienia bądź ostatecznie w jego trakcie. Wszystkie defekty wykryte w gotowej partii produktu lub – gorzej – zgłoszonej reklamacji są wyłącznie stratą dla zakładu i utratą reputacji.
Mimo istnienia w dwudziestym pierwszym wieku wielu innowacyjnych rozwiązań dla zakładów produkcyjnych, takich jak inteligentne oprogramowania, zrobotyzowane gniazda, zintegrowane systemy kontroli produkcji, wciąż pojawiają się głosy, iż ilość jest bardziej dochodowa niż jakość. Właściciele zakładów obawiają się włączenia automatyzacji ze względu na wiążące się z tym koszty. Te z kolei, przekładając się na cenę towaru, mogą odstraszyć ich dotychczasowych klientów mimo nadrzędnego celu, jakim jest poprawa jakości.
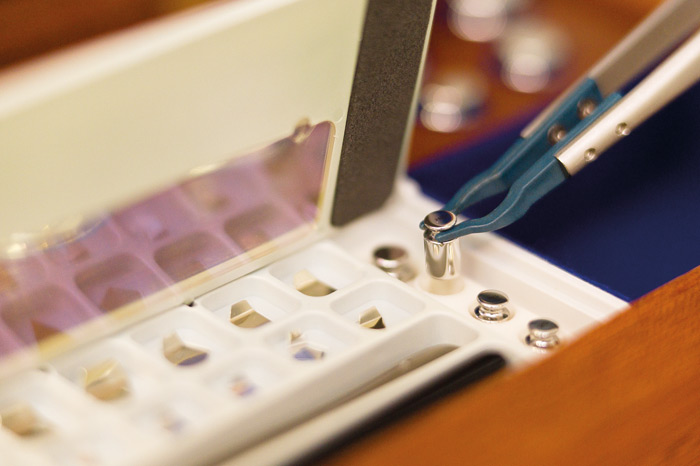
Pytanie, nad jakim należy się zastanowić w takiej sytuacji, to jaka opcja przyniesie mierzalne zyski dla przedsiębiorstwa długoterminowo?
Braki w audycie stanów magazynowych mogą rodzić pytania u kierowników produkcji, na jakim etapie doszło do strat. Defekty w działaniu, inny kolor czy złe wymiary – wszystko to jest sygnałem dla pracowników, że standardy kontroli w zakładzie zawiodły. Gdzie więc mogą leżeć źródła problemów? Najczęściej jest to zła organizacja czy nieskuteczny system zarządzania, błąd pracownika, niedoświadczona kadra, nieodpowiednio dostosowana maszyna, zły lub zanieczyszczony surowiec, źle odmierzone proporcje komponentów, a także zniszczenia poszczególnych elementów maszyn, niezauważalne na pierwszy rzut oka. Przyczyny odchyleń można podzielić na dwie kategorie: organizacyjne, które ciężej zweryfikować i zmienić, wymagające znacznego zaangażowania kadr, a także techniczne, które prościej wskazać, jednak ich poprawa wiąże się z wyższymi kosztami.
Tempo rozrastania się gospodarki nie jest pobłażliwe dla przedsiębiorstw, które nie przestrzegają pewnych standardów.
Współczesny konsument jest coraz bardziej świadomy, zwraca uwagę na to, co kupuje i od kogo, nie wybiera produktów szkodliwych dla środowiska, a tym bardziej dla siebie. Poprzeczka jakości jest postawiona wysoko i wszyscy producenci chcący pozostać konkurencyjni muszą spełniać określone wymagania dla danej branży.
Wspomniane wcześniej systemy zarządzania jakością to, ogólnie ujmując, zbiór norm, których celem jest osiągnięcie określonych celów jakości. Mogą się one odnosić do wyników osiąganych przed przedsiębiorstwo, do funkcjonowania firmy, kultury organizacyjnej czy klienta. W różnych obszarach gospodarczych inne normy grają pierwszorzędną rolę, zależnie od wytwarzanych dóbr, ich przeznaczenia i rodzaju ostatecznego konsumenta. Najbardziej znana w gospodarce jest międzynarodowa standaryzacja ISO, postrzegana jako wysoka wartość biznesowa dla każdego przedsiębiorcy. ISO 9001 określa ogólne standardy jakości, ISO 13485 przeznaczona jest dla wyrobów medycznych, ISO 22000 do żywności i wiele innych – wszystkie stanowią wyznaczniki w procesie automatyzacji przemysłu. Posiadając certyfikaty ISO, firma osiąga prestiż i konkurencyjność na rynku, może liczyć na większe zyski i możliwość bycia liderem w swoim sektorze rynku.
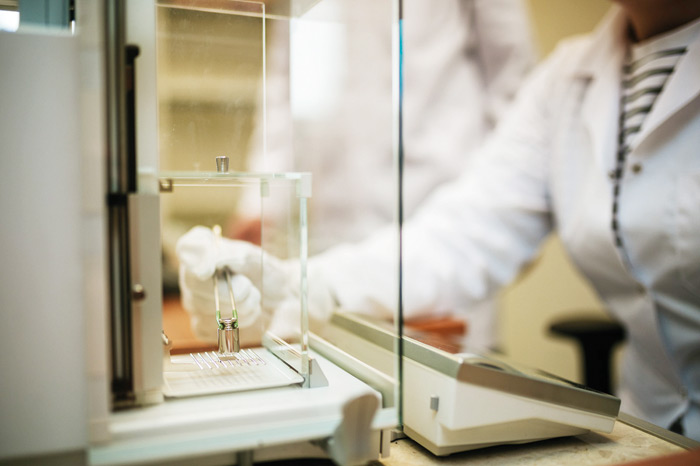
W procesie standaryzacji i wyznaczania jakości produkcji branża farmaceutyczna jest przykładem, gdzie wymagania jakościowe od dawna realizowane są na najwyższym poziomie.
Dla farmacji przewodnikiem po świecie jakości jest między innymi Farmakopea, która określa podstawowe wymagania jakościowe dla leków znajdujących się na rynku farmaceutycznym na danym terytorium. W Polsce obowiązuje Farmakopea Polska i jej nadrzędna Europejska, pod którą podpisało się 8 państw europejskich. Zgodnie z zapisami Farmakopei Europejskiej jej celem jest polepszanie zdrowia publicznego dzięki wprowadzaniu na rynek produktów leczniczych i ich składników spełniających określone wymagania jakości. Dodatkowo jej realizacja ma ułatwiać bezpieczny przepływ leków na terenie Europy i poza nią.
Obowiązek spełniania standardów farmakopealnych zapisany jest także w polskim Prawie farmaceutycznym – (art. 25) Podstawowe wymagania jakościowe oraz metody badań produktów leczniczych i ich opakowań oraz surowców farmaceutycznych określa Farmakopea Europejska lub jej tłumaczenie na język polski zawarte w Farmakopei Polskiej.
Na samym początku postawiliśmy hipotezę: „Nieodłącznym elementem realizacji działalności w przemyśle, a przede wszystkim w zakładach produkcyjnych, są narzędzia pomiarowe”.
Odpowiednia ilość komponentów odmierzonych przez wagi automatyczne i nieautomatyczne jest kluczowa w ocenie zgodności wyrobu końcowego z założoną specyfikacją. Współczesne rozwiązania w zakresie ważenia wykorzystują wagi elektroniczne, w których informacje wyświetlają się na monitorach, panelach HMI i mogą być przekazywane do współpracujących maszyn. W obliczu takich możliwości wagi mechaniczne nie są już powszechnie używane, użytkownicy wybierają praktyczność i inteligentne rozwiązania.
Dziś coraz większe znaczenie ma gromadzenie wszelkich danych, w przypadku przemysłu – tych pozyskiwanych z pomiaru wagi i maszyn. Wykorzystywane dane są współdzielone pomiędzy różnymi maszynami i systemami, ułatwiają planowanie produkcji, kontrolę przebiegu, usprawnianie procesów i oddelegowania pracowników. Dlatego ważne jest, by transmisja informacji była niezawodna, co więcej – precyzyjna i wiarygodna.
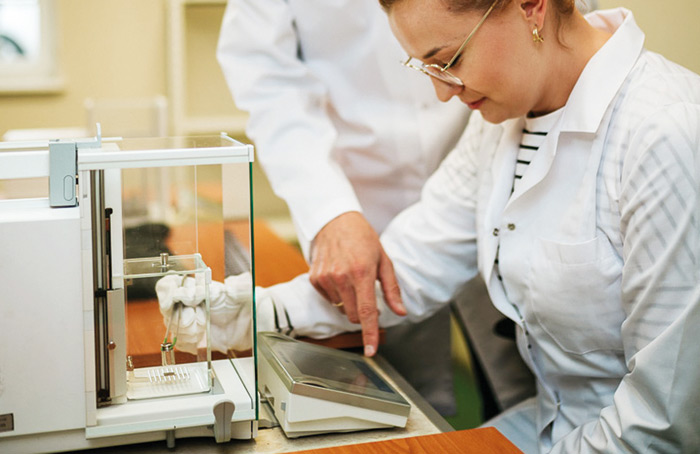
Studium przypadku.
Przykładów błędów produkcyjnych można by wymienić wiele i wskazać ich źródło. Takie, które są konsekwencją stosowania niezweryfikowanych technicznie narzędzi pomiarowych możemy znaleźć w każdym sektorze gospodarki.
Na produkcji farb, przy mieszaniu odpowiednich dawek barwników nie ma miejsca na błędy, ostateczny kolor musi być identyczny z celowym. Co więc jeśli np. waga automatyczna w tym zakładzie pokazuje inny wynik pomiaru niż rzeczywista waga materiału? Cała seria musiałaby zostać odrzucona lub poprawiona, co wiąże się z dodatkowymi kosztami, a mimo to użytkownik mógłby wciąż nie być świadomy, gdzie leży źródło problemu. Kolejnym przykładem jest produkcja proszków do prania – dodanie nieodpowiedniej ilości danej substancji chemicznej może całkowicie zmienić działanie końcowego wyrobu – proszek działałby wybielająco zamiast prać. Odnosi się to także do całej branży farmaceutycznej i kosmetycznej, gdzie zastosowania produktu określone są często listą przeciwwskazań do użytku i potencjalnymi alergenami. Weźmy pod lupę na przykład krem do twarzy z kwasem na niedoskonałości, do którego podczas produkcji waga dodała więcej substancji kwasu, niż było to określone w specyfikacji. Taka sytuacja może mieć miejsce, jeśli narzędzie pomiarowe waży z błędem – wskazuje niższy wynik pomiaru. Taki krem mógłby spowodować silne podrażnienie skóry, przesuszenie lub nawet poparzenie, co skutkowałoby potężnymi konsekwencjami prawnymi i finansowymi dla producenta. Jeszcze poważniejszym przypadkiem są leki czy substancje stosowane np. w chemioterapii chorób nowotworowych.
Przy branży farmaceutycznej należy wspomnieć o zmianach w Farmakopei Europejskiej, która dla farmacji jest uznawana za normę. Rozdział 2.1.7 Balances for Analytical Purposes uaktualnionego wydania Farmakopei Europejskiej określa wzorcowanie jako część procesu kwalifikacji wagi w celu zapewnienia zgodności z wymaganiami w branży farmaceutycznej.
Innym przykładem są baterie, których komponenty, jeśli zostaną źle odmierzone w procesie, mogą w skrajnych przypadkach wybuchnąć podczas użytkowania. Każdy niedopatrzony błąd może kosztować życie. Natomiast z technicznego punktu widzenia najgorszym scenariuszem dla zakładu produkcyjnego jest otrzymanie grupowego zwrotu serii z reklamacją. Straty finansowe mogą sięgać kilkukrotnej inwestycji w dany projekt.
Jak więc zapobiegać takim rozwojom wypadków?
Odpowiedzią jest oczywiście przestrzeganie norm adekwatnych systemów zarządzania jakością oraz praktykowanie nadzoru metrologicznego. Nadzór, jak sama nazwa wskazuje, jest nieustannym procesem weryfikującym, w tym przypadku narzędzi pomiarowych pod względem wyników pomiarów i ich zgodności z przyjętymi parametrami granicznymi.
Nadzór metrologiczny powinien być praktykowany wszędzie tam, gdzie waga pełni istotną rolę – zwłaszcza w każdym procesie produkcyjnym. Wiąże się to z dyscypliną cyklicznych kontroli, serwisowania i skrupulatnego raportowania wszelkich odchyleń w działaniu maszyn. Pracownik odpowiedzialny za nadzór jest zobowiązany dbać o cykliczność wzorcowań wag i ich ocenę oraz inne czynności kontrolne pomiędzy kolejnymi kalibracjami w celu zapewnienia spełnienia wymagań metrologicznych.
Dla wspomnianej zmieniającej się branży farmacji (laboratoria i produkcja farmaceutyczna) są to specjalnie opracowane wzorcowania wag oraz sprawdzenia dla farmacji. Z biegiem czasu i rozwoju gospodarki rola właściwego nadzoru metrologicznego zaczęła być tam coraz bardziej dostrzegana. Pierwsze zmiany w tym zakresie wprowadziła Farmakopea Amerykańska, za którą podążyła Farmakopea Europejska, podkreślając w swoich zapisach rolę wzorcowania wag, precyzji, dokładności pomiarów oraz niepewności z tym związanej w procesie badania chemicznych i biologicznych substancji leczniczych oraz w sposobie dawkowania, a także sprecyzowała metody analizy leków. Otwiera to nowy rozdział w zakresie tematyki wzorcowania wag przez Laboratoria wzorcujące na potrzeby farmacji. Być może za tym przykładem pójdą inne normy i wytyczne, które doprecyzują znaczenie wzorcowania w procesie nadzoru metrologicznego.
Wspomniane wzorcowanie, które w procedurach nadzoru metrologicznego pełni najważniejszą rolę, jest wykonywane przez Akredytowane Laboratoria Wzorcujące i dla nich jest rutynowym działaniem. Dzięki wzajemnej współpracy Laboratorium wzorcującego z użytkownikiem wbrew pozorom będzie ono prostym procesem z punktu widzenia użytkownika. Jego efektywność dla przedsiębiorstwa będzie zależała jednak od regularności i dostosowania planu produkcji do wyników dostarczonych przez laboratorium.
Jak często należy więc wzorcować wagę?
Obowiązek wzorcowania, w porównaniu do legalizacji nie jest zdefiniowany prawnie. Analogicznie, nie jest więc narzucona optymalna cykliczność przeprowadzania wzorcowania. Decyzja w tej kwestii leży po stronie użytkownika wagi, który powinien rozważyć jej parametry, jakość, wpływ na środowisko i oszacować ryzyko. Przez oszacowanie ryzyka można rozumieć zużycie sprzętu i częstotliwość przeglądów i napraw, systematyczne kontrole i wykonane wzorcowania czy adiustacje.
Jak w praktyce wygląda proces wzorcowania wagi?
Technik sprawdza wynik ważenia dla kilku czy kilkunastu punktów pomiarowych przy pomocy wzorców masy (odważników). Różnica pomiędzy wartością wskazania a wartością obciążenia (wzorcami masy) jest podstawą obliczenia błędu pomiaru wraz z jego niepewnością. Najczęściej, w celu zobrazowania użytkownikowi wagi wyników wzorcowania, przedstawia się je w postaci wykresów oraz tabelek. Na podstawie wyżej wymienionych wyników użytkownik wagi może zastosować odpowiednie korekty w celu uzyskania poprawnej wartości ważonego produktu.
Jakie są korzyści z przeprowadzonego wzorcowania?
Przede wszystkim jest to możliwość dopasowania planu produkcji i zużycia komponentów. Formalnym poświadczeniem odbytej kalibracji jest Świadectwo Wzorcowania wystawione przez Akredytowane Laboratorium Wzorcujące, które przeprowadzało procedurę. Świadectwo Wzorcowania dostarcza informacji o wartościach metrologicznych wzorcowanego przyrządu pomiarowego, czyli relację pomiędzy wzorcem a wskazaniem przyrządu wraz z jego niepewnością.
Wpisanie wzorcowania jako elementu nadzoru metrologicznego w zakładzie produkcyjnym daje możliwość wdrażania działań optymalizacyjnych na poszczególnych etapach ważenia, co w dłuższej perspektywie przynosi zwiększoną jakość produktów, zmniejszenie częstotliwości poprawek, brak problemów z audytem czy bardziej precyzyjne przewidywania używalności komponentów.
Wzorcowanie można więc określić jako jeden z kluczowych elementów prowadzących do automatyzacji produkcji. Akredytowane Laboratorium Wzorcujące KASPO LAB bierze czynny udział jako prelegent w sympozjach i konferencjach technicznych skupiających przedsiębiorców rozwijających się w duchu Przemysłu 4.0. Wdrażanie innowacyjnych rozwiązań w celu automatyzacji produkcji jest tam tematyką przewodnią, a ujęcie wzorcowania wag w programach tylko potwierdza, że kontrola narzędzi pomiarowych to punkt wiodący do automatyzacji i poprawy jakości.
Początki działalności KASPO LAB w dziedzinie pomiarów masy sięgają 1990 roku, a już od 2002 roku, jako pierwsi w Polsce, otrzymali akredytację PCA w zakresie wzorcowania wag i wzorców masy na potrzeby przemysłu: motoryzacyjnego, budowlanego, metalowego i metalurgicznego, chemicznego, kosmetycznego, farmaceutycznego, energetycznego, ciepłownictwa, papierniczego, tytoniowego, górniczego, spożywczego, elektroniki, gospodarki wodno-ściekowej, jednostek badawczo-rozwojowych, laboratoriów badawczych, jednostek kontrolujących. Ponadto zajmują się także sprzedażą urządzeń, szkoleniami i doradztwem technicznym.
KASPO LAB, podążając za zmianami rynkowymi i możliwościami doskonalenia procesów, oferuje kompleksowe wykonanie usług zgodnie z obowiązującymi regulacjami prawnymi i standardami jakości. Już 20 lat doświadczenia i pracy pod najszerszym zakresem akredytacji PCA pozwoliło rozwijać się w swojej specjalności wraz z klientami – zakładami produkcyjnymi. Z biegiem lat zmieniały się wymagania przedsiębiorstw odnośnie do kontroli pracy i efektów, mierzenia korzyści, także tych płynących z nadzoru wag. Tak o pracy w dziedzinie pomiarów wypowiada się jeden z techników KASPO LAB:
– Gdy Kaspo Lab rozpoczynało swoją działalność, wagi były wybierane najczęściej na podstawie dwóch parametrów: dokładności odczytowej (d) oraz maksymalnego udźwigu (max). Z biegiem lat obserwowaliśmy, jak i sami przyczynialiśmy się do wzrostu świadomości użytkowników odnośnie do ważenia oraz jego wpływu na procesy produkcyjne i badawcze. Użytkownicy wag w przemyśle, laboratoriach zaczęli dostrzegać wymierne korzyści finansowe, jakościowe, które przekładały się na ogólną rentowność produkcji oraz badań. Dziś można mówić o rodzącym się procesie w zakresie zakupu nowej wagi i późniejszego jej użytkowania.
Obecnie zakłady produkcyjne mogą wybierać w rozwiązaniach mających na celu poprawić jakość i wydajność produkcji.
Lista opcji zaczyna się od tych najbardziej zaawansowanych i innowacyjnych, do tych, które można wprowadzić z dnia na dzień bez zaangażowania zewnętrznych zasobów. Podstawowym krokiem jaki winien podjąć kierownik produkcji jest weryfikacja zestawień danych o maszynach, procesach, pracownikach, programach. Sposób i zakres gromadzenia danych jest podłożem do podjęcia i planowania pracy zakładu. Nieefektywna też w obecnych czasach jest dokumentacja papierowa – dane powinny być przechowywane w chmurze, ogólnodostępne dla pracowników, bez ryzyka ich utracenia. Dane także powinny zawierać informacje o stanie maszyn, serwisowaniach, ew. odchyleniach w działaniu, gwarancji. By uniknąć awarii maszyn mogących spowodować znaczny przestój w pracy, należy regularnie szacować ich wydajność i sprawność. Złotą zasadą jest także skracanie czasu pracy tam, gdzie to możliwe, zamienianie rąk ludzkich na maszyny i roboty oraz informatyzowanie procesów. Kolejnym aspektem jest nieoszczędzanie na jakości produktów, dzięki któremu masz pewność, że nie stracisz klienta, a wzrośniesz na rynku. Jeśli chodzi o jakość wyrobu, najistotniejsze są tutaj surowce i komponenty oraz narzędzia pomiarowe, nad którymi powinien być prowadzony nadzór metrologiczny. Następną kwestią jest organizacja – czyli ogólnie pojęte planowanie pracy, rozkład zleceń, zajęcie maszyn, logistyka dostaw i odbiorów. Wiąże się to ściśle z zatrudnieniem i monitorowaniem pracy całego zespołu.
Bardziej wymagającym posunięciem jest zwiększanie kompetencji firmy i zespołu, zaczynając od międzynarodowych standardów jakości, takich jak normy ISO, po różnego rodzaju certyfikacje i akredytacje, ordery. Nowe technologie z kolei oferują szereg oprogramowań mających na celu stworzyć gałęzie połączeń między maszynami i umożliwić zdalne, scentralizowane sterowanie produkcją. Tutaj coraz popularniejszą rolę odgrywają także zrobotyzowane gniazda produkcyjne, które zastępują pracę robotnika fizycznego i eliminują potencjalne błędy ludzkie.
Należy pamiętać, iż w idealnej wizji pracy zakładu produkcyjnego nie zabraknie miejsca na błędy, które mogą się zdarzyć nawet niezależnie od czynnika ludzkiego. Mówiąc o optymalizacji, cyfryzacji i automatyzacji produkcji oraz poprawie jakości wyrobu, wskazuje się odpowiednie zalecenia. Mają one na celu wyeliminowanie, ale przede wszystkim znaczne zmniejszenie ryzyka wystąpienia błędu. Taka sama zasada odnosi się do narzędzi pomiarowych – po wykonanym wzorcowaniu można poddać wagę adiustacji, czyli korekcji wskazań wagi. Korekcja ta nie sprawi jednak, że waga będzie wskazywała stuprocentowo wiarygodny wynik pomiaru. Ponowne wzorcowanie po adiustacji wskaże, z jakim maksymalnie błędem waga waży. Celem korekcji jest więc zmniejszenie potencjalnego błędu pomiaru, ale nie jest możliwa korekcja do pełnego wyeliminowania błędu. Stąd nadzór metrologiczny jest tak ważny, bieżąca kontrola urządzeń pozwala przewidzieć i określić zapotrzebowanie magazynowe oraz zlikwidować potencjalne straty.
KASPO LAB Sp. z o.o.
Laboratorium Wzorcujące Wagi i Wzorce Masy
Akredytacja PCA nr AP 043
tel. 58 556 78 82
www.KASPOLAB.com
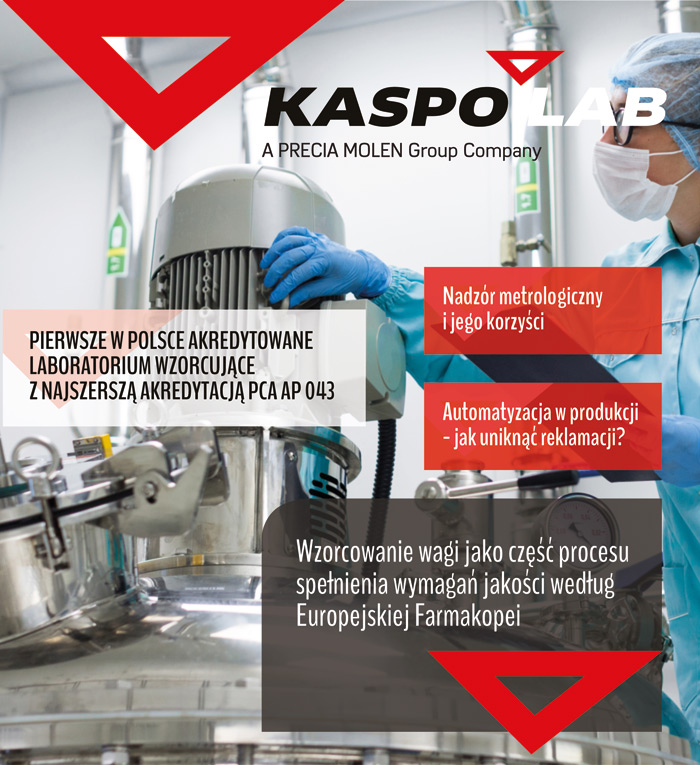