Linia do wytwarzania wysokojakościowego regranulatu z własnych odpadów produkcyjnych folii z ...
Linia do wytwarzania wysokojakościowego regranulatu z własnych odpadów produkcyjnych folii z nadrukiem w obiegu zamkniętym, w firmie POLIPAKStreszczenie: Omówiono technologię wytwarzania wysokojakościowego regranulatu z własnych odpadów produkcyjnych folii z nadrukiem w obiegu zamkniętym. Proces produkcyjny w obiegu zamkniętym zapewnia przetworzenie i powtórne wykorzystanie 100% odpadów własnych, powstających w przedsiębiorstwie. Opisano prototyp automatycznej, innowacyjnej instalacji demonstracyjnej linii produkcyjnej do produkcji regranulatu, pozwalającej na efektywne połączenie wszystkich etapów przetwarzania odpadu produkcyjnego, w tym dzięki zwiększeniu stopnia automatyzacji (roboty AGV) poszczególnych etapów procesu recyklingu. Instalacja pracuje w nowo budowanym zakładzie produkcyjnym w Środzie Wielkopolskiej.
Słowa kluczowe: automatyzacja, recykling, folia, Przemysł 4.0.
Wstęp
Artykuł dotyczy najnowszych determinant rozwojowych w obszarze „ZERO ODPADÓW Z TWORZYW SZTUCZNYCH” (rys. 1), do których należą: folie z tworzyw sztucznych: PE - polietylen, PE-LD - polietylen niskociśnieniowy, PE-HD - polietylen wysoko ciśnieniowy, PP - polipropylen (odmiana orientowana OPP), PS - polistyren, PS-E - polistyren spieniony (styropian), PW - poliwęglany; PCW (PVC) - polichlorek winylu, PETF - poliestry, PA - poliamid, materiały opakowaniowe - wielowarstwowe (kompozyty, tworzywa kompleksowe). Przy czym tradycyjnie wykorzystuje się jako tworzywa opakowaniowe: drewno i tworzywa drzewne, materiały roślinne niedrzewne (wiklina, maty), metale i folie metalowe, wyroby papiernicze (papiery, tektury, celofan-folia celulozowa), surowce włókiennicze (juta, len, konopie, włókna syntetyczne), ceramika. [4, 5].
Rozwiązania związane z odpadami opakowaniowymi, w tym z tworzyw sztucznych, pozyskuje się jednocześnie stosując ekobilans. Zakładając, że dla wszystkich opakowań powinien być opracowywany i obejmować pełną drogę życia zwaną często LCA (Life Cycle Analysis), począwszy od pozyskania surowca przez produkcję, aż do dystrybucji, konsumpcji i usunięcia pozostałości, łącznie z utylizacją. Elementy składające się na procesy, produkty, czynności i ich warianty przy opracowaniu bilansów ekologicznych nazywa się często umownie modułami (jak na rys. 1).
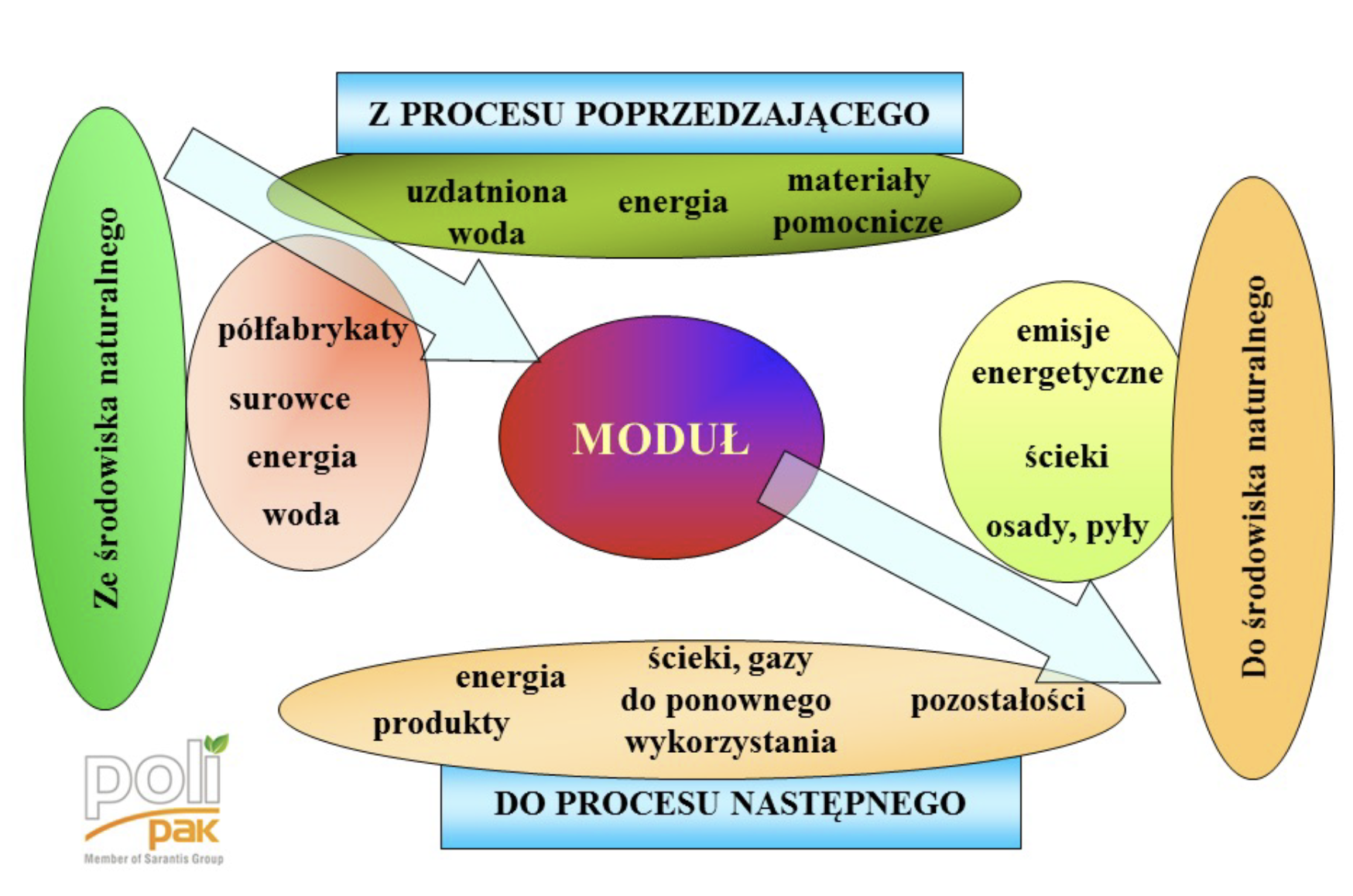
Rys. 1. Opakowania w systemach logistycznych - aspekty ekologiczne opakowań. Oprac. własne
Polipak Sp. z o.o., jest firmą przetwarzającą polietylen, zarówno w postaci regranulatu (polietylenowe surowce wtórne) jak również w postaci surowca pierwotnego (polietylen typu „virgin”) do produkcji worków na odpady frakcyjne oraz komunalne. Dynamiczny rozwój firmy oraz ograniczenia unijne w zakresie przetwarzania polietylenu wprowadziły w przedsiębiorstwie nowy sposób myślenia oraz orientację biznesową ukierunkowaną na pozyskiwanie surowca zarówno z odpadów polimerowych jak i z surowców pochodzenia naturalnego. Na skutek tych działań, znacząco rozbudowano wewnętrzny dział badawczo – rozwojowy (B+R). Wykorzystując środki własne oraz wsparcie z Narodowego Centrum Badań i Rozwoju (NCBiR), zaproszono do współpracy naukowców konstruktorów, projektantów oraz techników z wielu uczelni technicznych w całym kraju.
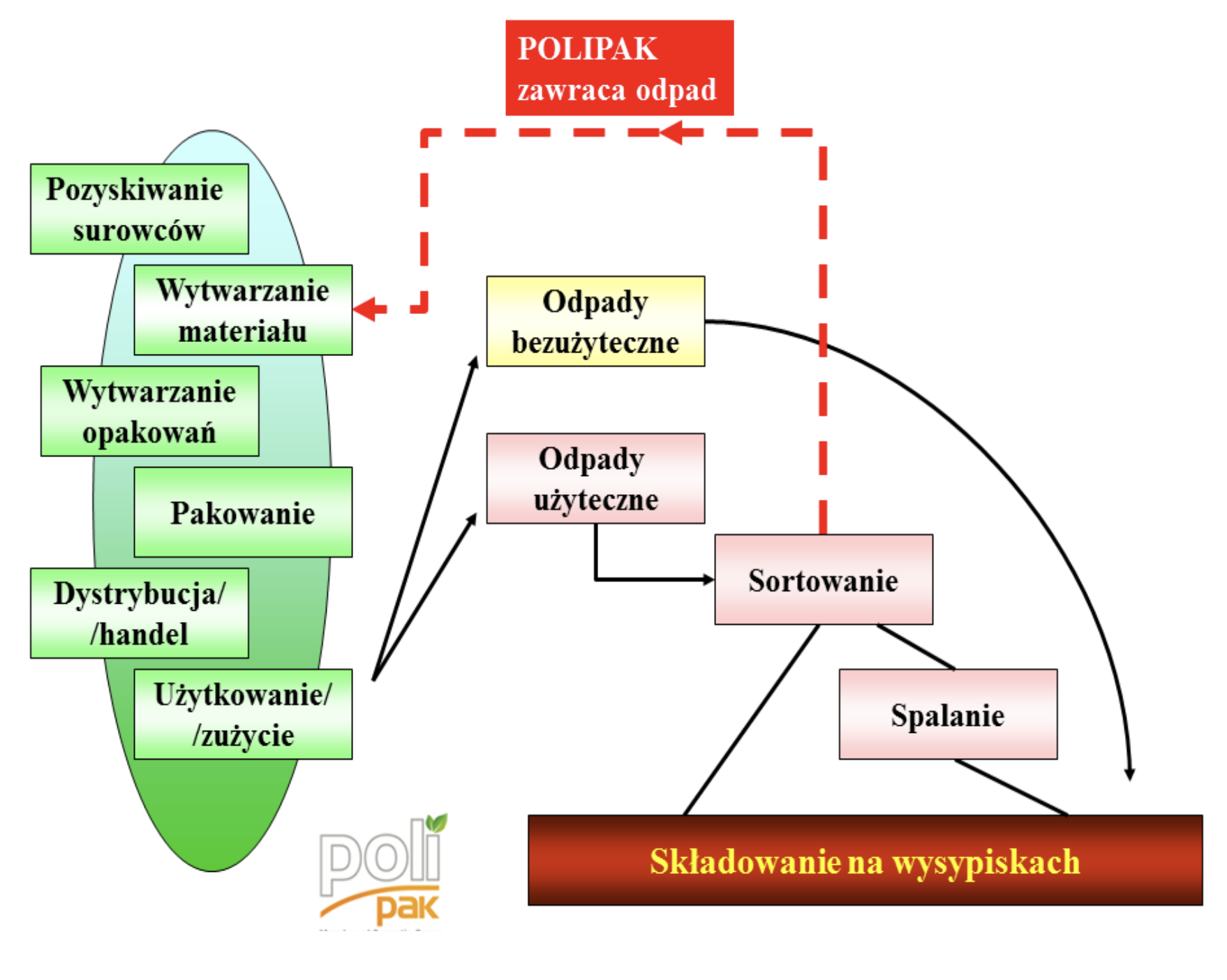
Rys. 2. Istota „zawrócenia odpadu” w firmie Polipak
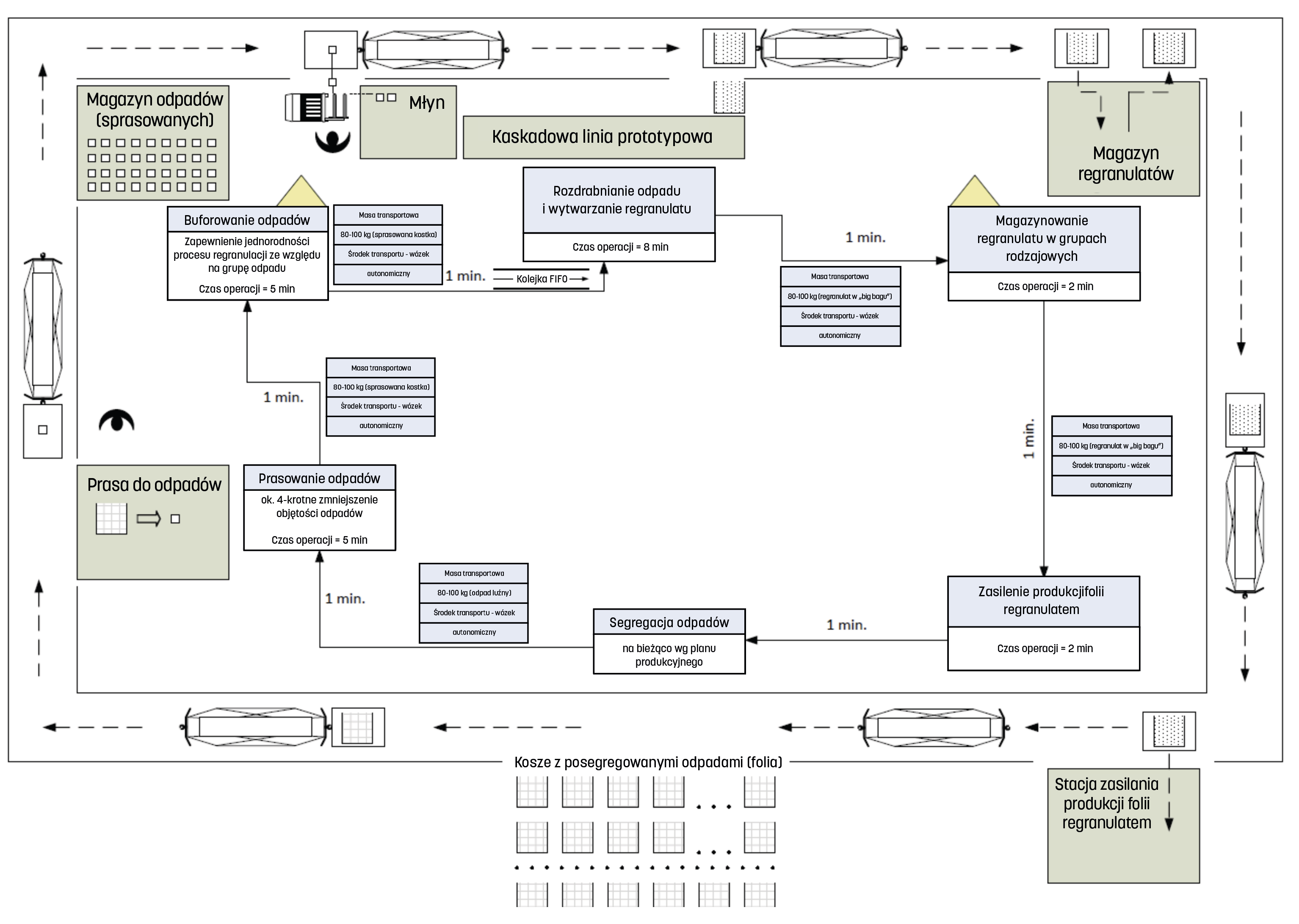
Rys. 3. Layout automatycznej linii recyklingu – poziom koncepcji
Inicjowane są obecnie działania Polipaku na rynku surowca, tworzyw sztucznych zauważalny jest wzrost zainteresowania odpadami, a przede wszystkim ich przetwórstwem, rys. 2. To wpływa na kształtowanie i zmiany przyzwyczajeń ludzi, a szczególnie sposób myślenia w odniesieniu do generowania odpadów przetwarzanych z polimerów, co z kolei prowadzi do redukcji śmieci w postaci chociażby zużytych worków foliowych – w zakresie niewyrzucania woreczków foliowych, podobnego poszanowania jak dla makulatury, dla której przecież w Polsce nie ma rynku wtórnego przetwórstwa odpadów. [6, 7]
1. Koncepcja innowacyjnej linii recyklingu odpadów
Automatyczna linia recyklingu działa w reżimie selekcji odpadu produkcyjnego na grupy [4], a następnie przeprowadza się efektywne oczyszczanie tworzywa odpadowego dzięki wykorzystaniu mechanicznego filtrowania stopionego tworzywa poprzez zastosowanie kaskadowego układu wytłaczarek w linii technologicznej recyklingu według własnego rozwiązania technologicznego. Dzięki wewnętrznej selekcji niepełnowartościowe worki stanowiące odpad produkcyjny dzieli się na grupy, uwzględniając:
- rodzaj tworzywa (LD-PE, MD-PE, HD-PE),
- jego skład (kolor, zawartość dodatków),
- powierzchnię nadruku naniesionej na folię.
Precyzyjnie realizowana selekcja odpadu wyeliminuje przypadkowe mieszanie różnych rodzajów tworzyw, co jest podstawową przyczyną problemów z przetwórstwem regranulatu pozyskiwanego od producentów zewnętrznych.
Oczywiście nie byłoby to możliwe bez wprowadzenia wielu szkoleń dla pracowników – nie tylko chodzi o pracowników zatrudnionych bezpośrednio na produkcji. Przemysł 4.0 zmienia całkowicie styl pracy w całej firmie, każdy pracownik musi rozumieć, jak ważna jest jakość regranulatu oraz że każdy pracownik ma wpływ na jakość wyrobów finalnych.
Ponadto wprowadzono w obszarze automatycznej linii regranulacji system automatycznej identyfikacji odpadu na każdym etapie oraz stale aktualizuje się bazę odpadów na potrzeby automatycznej linii regranulacji. Do kodowania grupy odpadu zastosowano odpowiedni wektor informacji kodowany w formie kodu kreskowego, który stosuje się do znakowania odpadu.
Badania wykazały, że opłacalne jest wprowadzanie na linię regranulacji tzw. masy krytycznej odpadu, której przetwarzanie jest opłacalne. Ponieważ w POLIPAK’u realizowane są zróżnicowane zlecenia produkcyjne, dlatego zaprojektowano w ramach automatycznej linii regranulacji moduł wstępnej aglomeracji odpadów, którego działanie polega na zmniejszaniu jego objętości poprzez prasowanie przy jednoczesnym formowaniu w kostkę prostopadłościenną, a powstałą kostkę zabezpiecza się przed rozformowaniem, tak by w procesie transportu „do” lub „z” magazynu buforowego odpadu, jak też w procesie składowania nie ulegała rozformowaniu. Kostki znakuje się kodując informacje o odpadzie sprasowanym oraz masie. To pozwala efektywnie zmniejszyć również przestrzeń niezbędną do składowania odpadu w przestrzeni magazynu buforowego. Przestrzeń magazynu jest podzielona na miejsca odkładcze analogicznie jak w magazynach zintegrowanych jednostek ładunkowych i oznaczona kodem lokalizacyjnym, powiązanym z konkretną kostką, tak że możliwe jest monitorowanie kostki odpadu w procesie składowania. Odpad np. w kolorze odbiegającym od przetwarzanego na linii jest buforowany – tzn. przechowywany do momentu, gdy jest potrzebny lub po uzbieraniu się odpowiedniej ilości danego rodzaju odpadu i skierowaniu go na kaskadę linii regranulacji.
Przedmiotowa automatyczna linia recyklingu spełnia wyzwania stawiane określeniu „Przemysł 4.0”. Oznacza to, że wszystkie operacje technologiczne i produkcyjne są sterowane automatycznie, a praca operatorów ma charakter operacyjno-kontrolny, rys. 3.
Roboty mobilne dostarczają folię odpadową z linii produkcyjnych POLIPAK’u do magazynu buforowego. Za pomocą wózków robotów AGV lub jeżeli objętość magazynu na hali zostanie wypełniona – do dodatkowego magazynu na zewnątrz hali – wózkiem widłowym wyposażonym w łapy pozwalające sprawnie przemieszczać uformowane kostki folii.
Po uzbieraniu masy krytycznej odpadu z poszczególnych grup odpadów z bazy odpadów wybrane kostki sprasowanej folii są wywoływane do młyna linii regranulacji. Roboty mobilne lub wózek widłowy pobierają je z magazynu buforowego i dostarczają do młyna, gdzie dalej w toku technologii regranulacji rozdrobiony odpad dostarczany jest do kaskady wytłaczarek w celu oczyszczenia regranulatu z zanieczyszczeń.
Odpad folii dowieziony do prasy (belownicy) może bezpośrednio z wywrotnicy belownicy być skierowany do oczyszczenia na kaskadowej linii wytłaczarek.
Po oczyszczeniu regranulat gotowy do odbioru w big-bag’u robot AGV odwozi do magazynu regranulatu. Tam gdzie przechowany jest surowiec w POLIPAK’u zasilający przez centralny zasyp produkcję, zgodnie z recepturą wyrobu.
2. Problemy badawcze
Realizacja budowy demonstratora automatycznej linii regranulacji wymagała przeprowadzenia wielu badań przed zaprojektowaniem linii demonstracyjnej. Zrealizowano prace B+R w zakresie:
- badań chemicznych regranulatu (tworzywa): DSC, FTIR, MFI,
- badań wytrzymałościowych folii wytwarzanej z tworzywa zawierającego regranulat,
- prac rozwojowych związanych z integracją mechaniczną i softwareową elementów linii regranulacji,
- optymalizacji działania demonstratora automatycznej linii regranulacji.
Badania chemiczne regranulatu MFR, DSC, FTIR wykonuje w celu zbudowania bazy cech materiałowych ważnych dla uruchomienia wysokowydajnej linii regranulacji odpadów, która będzie spełniać kryteria nowoczesnych systemów recyklingu poprzez kontrolę jakości regranulatu, poprzez redukcję:
- substancji poprawiających przetwórstwo,
- pozostałości po napisach na opakowaniach produktów (w branży nazywanych resztkami farb),
- dodatków poprawiających współczynnik tarcia – dodawanych w procesach transportowo-spedycyjnych lub/i składowania,
- pozostałości celulozy,
- pozostałości klejów,
- innych tworzyw sztucznych (o innej temperaturze topnienia), które w wyniku błędu w sortowaniu znalazły się z polietylenem, jak: poliamid, poliestry i inne,
- drobin ziemi, piasku (kwarcu),
- pozostałości drewna,
- metali (kolorowych i stali),
- wilgoci (wody) i gazów.
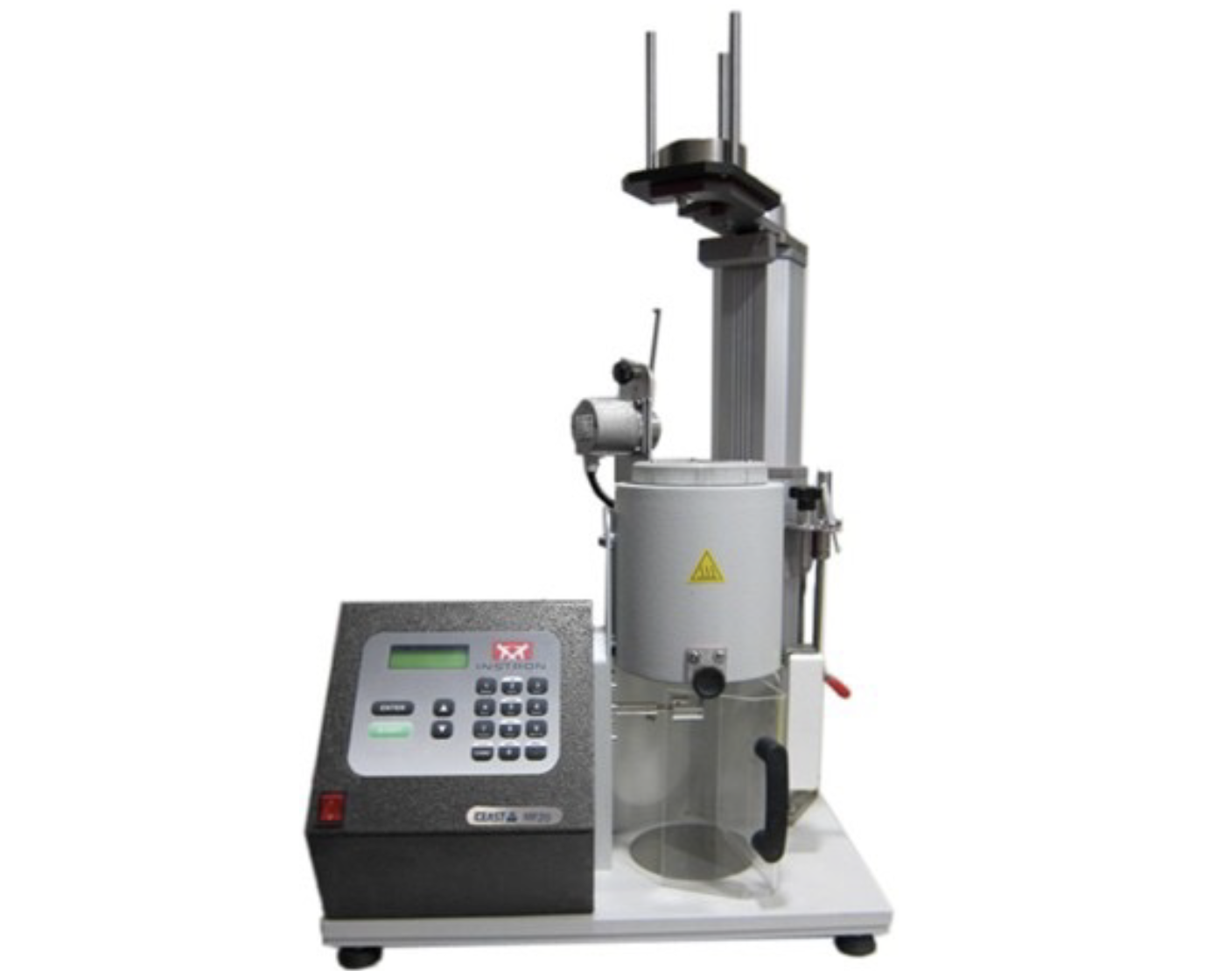
Rys. 4. Wygląd ogólny plastometru CEAST MF20
W wyniku tego procesu otrzymuje się regranulat niezależny od pochodzenia odpadu. Dlatego oczyszczenie go jest konieczne, ponieważ zanieczyszczenia utrudniają nie tylko proces technologiczny (np. zablokowanie rozdmuchu fragmentem metalu), ale też zakłócają stabilność produkcji (np. wadliwe/gorszej jakości produkty).
Powstawanie odpadu nie tylko w przetwórstwie tworzyw sztucznych nie musi się kojarzyć z niewłaściwym działaniem linii produkcyjnej lub błędów technologicznych w procesach produkcyjnych. Powstawanie odpadu jest normalne. Każdorazowe uruchomienie nowego zlecenia produkcyjnego wymaga ustawienia/dobrania parametrów technologicznych procesu, czy też kontroli jakości wyrobów prowadzonej metodami niszczącymi lub badań użytkowych.
Powstający odpad firma może wariantowo:
- Umieścić w wyżej opisanym systemie gospodarowania odpadami,
- Użyć go we własnej produkcji poprzez linię recyklingową - co firma POLIPAK realizuje.
Firma „zna swój” odpad, ponieważ przeszedł on przez jej linię produkcyjną. Zwykle wie więcej niż w momencie zakupu regranulatu na rynku, wyprodukowanym na bazie bardzo zróżnicowanym, przypadkowych odpadach poużytkowych tworzyw sztucznych. Mieszanie tak powstałego regranulatu z „własnego odpadu” z regranulatem kupionym staje się bardziej efektywne przy zachowaniu wysokich rygorów jakościowych produkcji.
Wskaźnik szybkości płynięcia należy do grupy użytkowych wskaźników przetwarzalności i jest podstawowym parametrem przetwarzalności termoplastycznych tworzyw polimerowych. Stosuje się go do oceny przydatności tworzywa do przetwórstwa metodami wtryskiwania i wytłaczania. Firma Polipak realizowała badania MFI we własnym laboratorium POLILAB na plastometrze firmy Instron, model CEAST MF20, rys.4.
Dane zarejestrowane podczas pomiaru przez plastometr są przekazywane do oprogramowania VisualMELT C-0710-650. Przykładowe wyniki zapisane w pliku *.csv pokazano na rys poniżej.
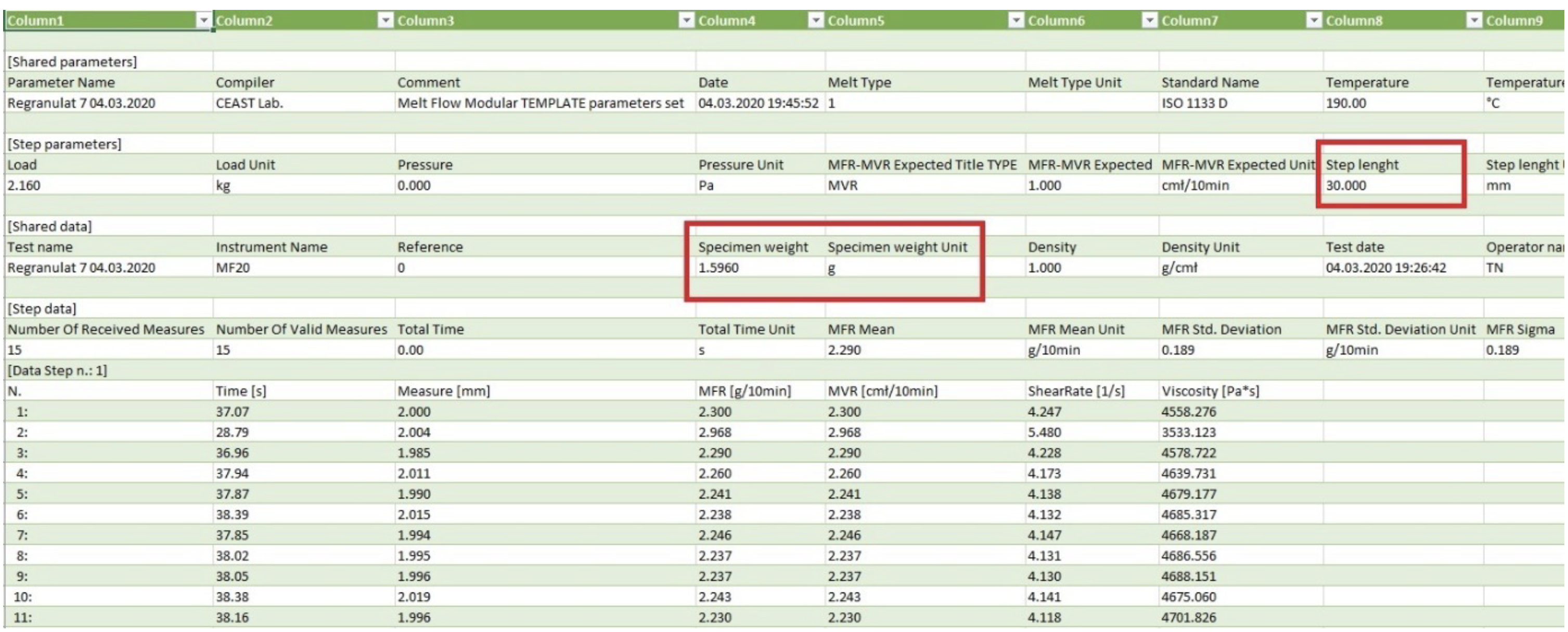
Rys. 5. Wygląd danych z plastometru zapisanych w postaci pliku.
Wyniki badań wskaźnika szybkości płynięcia dwóch tworzyw pierwotnych oraz ośmiu regranulatów zostały pokazane na rys. 4.
Wyniki badań gęstości w stanie stopionym zostały zamieszczone na wykresach rys. 6, 7, 8.
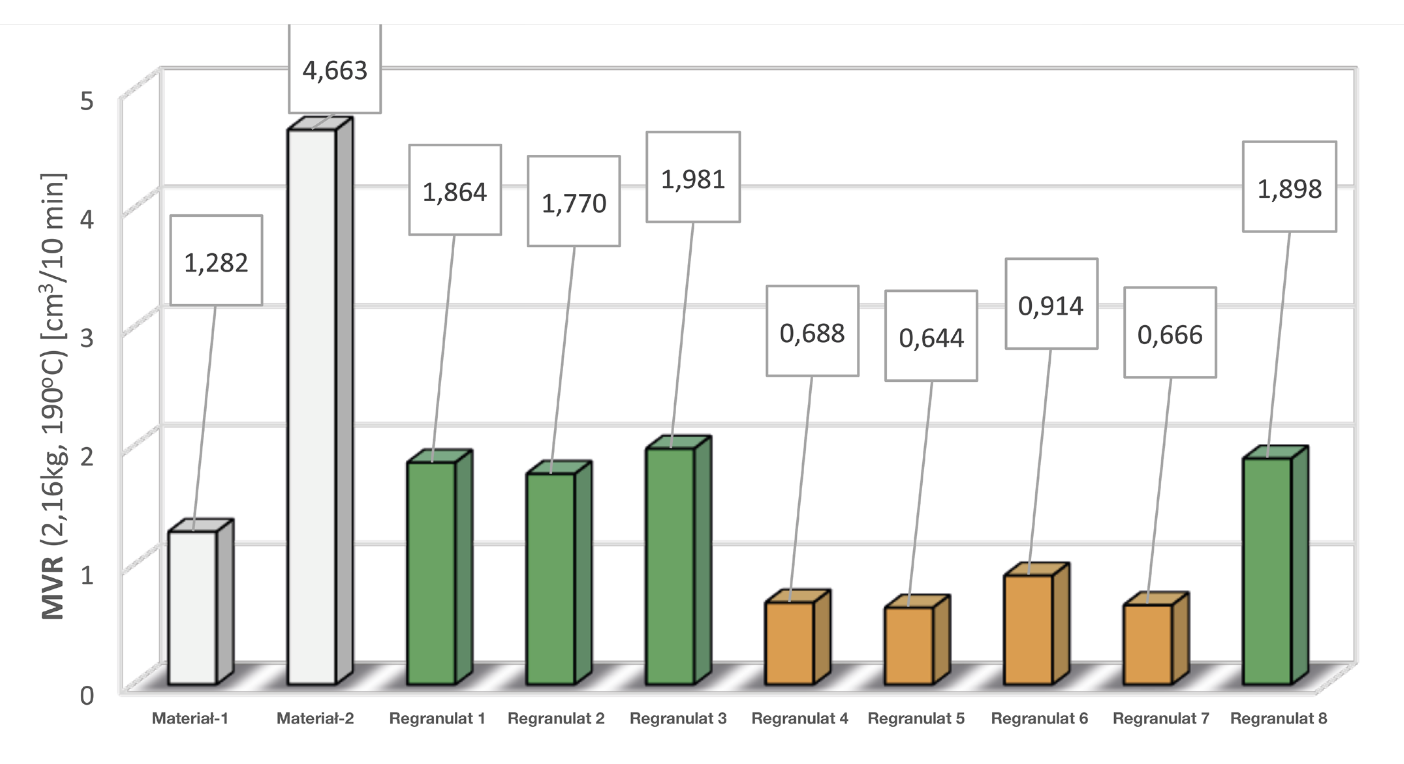
Rys. 6. Wartość objętościowego wskaźnika szybkości płynięcia tworzyw pierwotnych oraz regranulatów z polietylenu
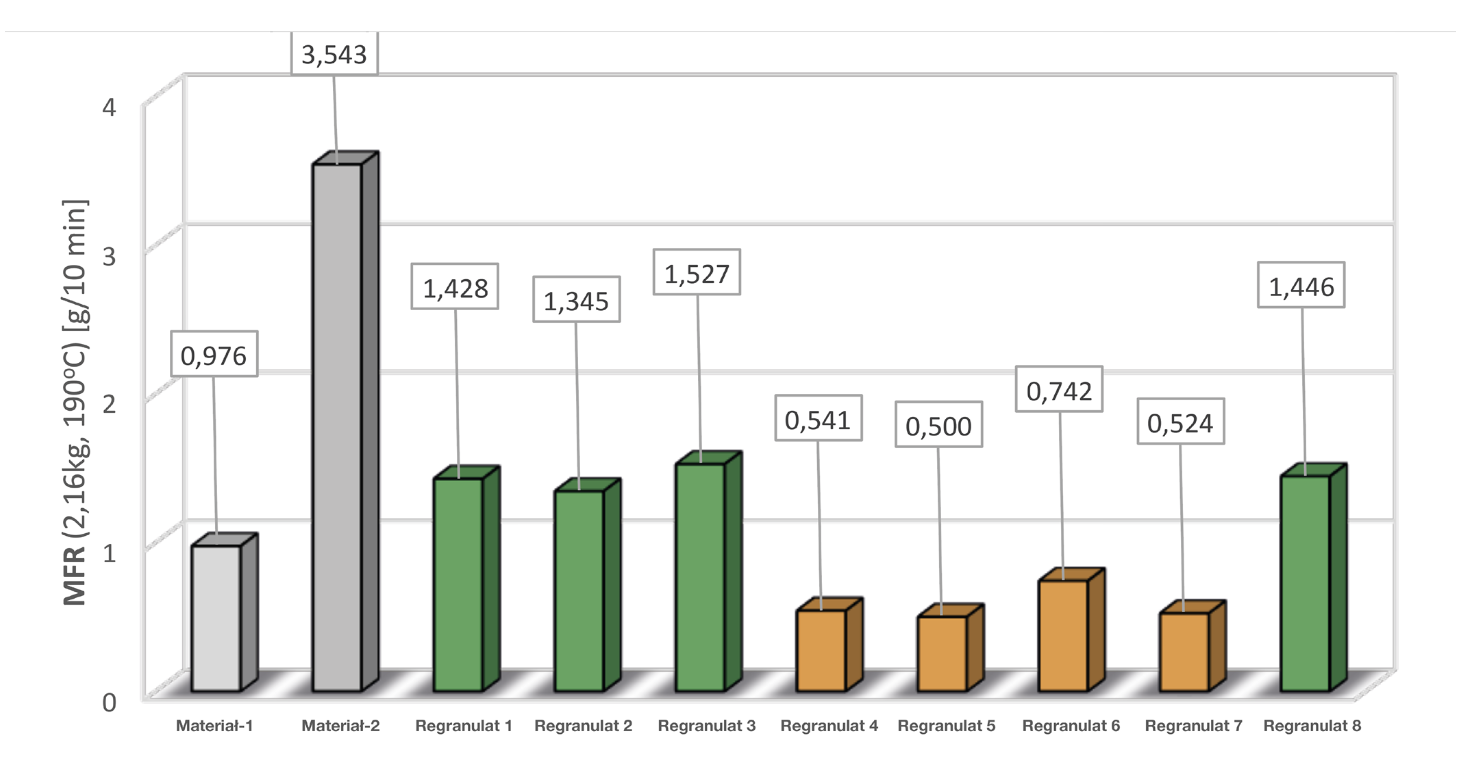
Rys. 7. Wartość masowego wskaźnika szybkości płynięcia tworzyw pierwotnych oraz regranulatów z polietylenu
Na wykresie 8 zestawiono wartości zbadanego masowego wskaźnika szybkości płynięcia z wartościami deklarowanymi przez dostawców i producentów. W przypadku polietylenu pierwotnego Materiał-1 (celowo ukryto nazwę producenta) oraz regranulatów 1, 3 i 6 były to wartości zgodne, w przypadku polietylenu pierwotnego Materiał-2 (celowo ukryto nazwę producenta) wartość zbadana była niższa o ok. 10% od wartości deklarowanej, natomiast w przypadku pozostałych regranulatów nie było możliwości porównania wyników.
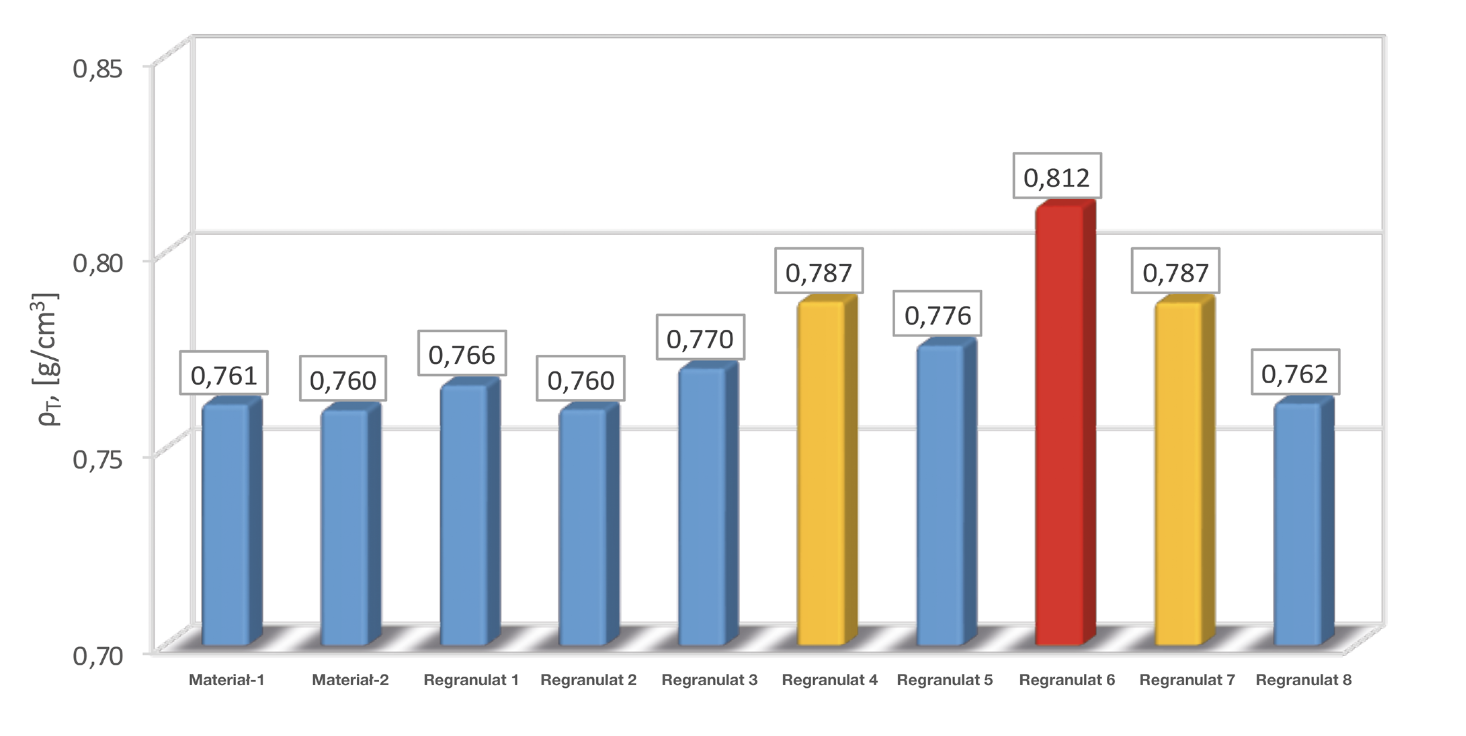
Rys. 8. Wartości gęstości w stanie stopionym tworzyw pierwotnych oraz regranulatów z polietylenu
W przypadku badań masowego wskaźnika szybkości płynięcia MFR (2,16 kg, 190°C) tworzyw pierwotnych potwierdzono wartość MFR (2,16 kg, 190°C) podaną przez producenta w przypadku polietylenu LD-PE Exceed. W przypadku polietylenu LD-PE Tipolen wykazano, że wartość zmierzona MFR (2,16 kg, 190°C)
była o ok. 10% mniejsza od wartości podanej w karcie materiałowej TDS.
Badania DSC i FTIR przeprowadzono w Laboratorium Chemicznym na Uniwersytecie Zielonogórskim. Dane te wypełniły cechy materiałowe bazy firmy POLIPAK.
Rezultaty badań regranulatu dostarczają szeregu informacji: jakościowych, technologicznych, chemicznych, wytrzymałościowych etc., które mają wartość nieocenioną z punktu widzenia przedsiębiorstwa, ponieważ mogą być wykorzystywane do tworzenia przewagi konkurencyjnej w branży producentów opakowań oraz do budowy i skalowania wysokowydajnej linii demonstracyjnej linii technologicznej.
Prace rozwojowe obejmowały zestawienie i konfigurację modułów instalacji w celu zapewnienia rzeczywistych sprzężeń pomiędzy nimi (w kontekście przepływu materiałów i sygnałów sterujących). Panuje takie przekonanie wśród menagerów, że wykonanie projektu, realizacja zakupu i dostawy maszyn zakończy już tylko pomyślna instalacja. Tymczasem należy pamiętać o integracji, która przebiega w dwóch płaszczyznach:
- technicznej, integracji zbioru maszyn,
- informacyjnej, przepływu informacji – tzw. software’owym.
Warto by prace były poprzedzone analizą numeryczną – np. POLIPAK zdecydował się na środowisko Flexim umożliwiającego projekcję modelu. Symulacja odwzorowuje rzeczywisty przebieg procesów logistycznych (z uwzględnieniem czasów operacyjnych i międzyoperacyjnych). Symulacje różnych wariantów pozwalają określić zależności pomiędzy parametrami (zarówno nastawczymi, jak również sterującymi) maszyn i urządzeń oraz określenie wpływu na zdefiniowane końcowe efekty procesu.
Do symulacji komputerowej zdefiniowano wszystkie maszyny i urządzenia odpowiedzialne za realizację operacji oraz czynności technologicznych i ich możliwości nastawcze, mające wpływ na kluczowe, zdefiniowane parametry procesu produkcyjnego przy założeniu wydajności automatycznej linii regranulacji.
Dane procesów operacyjnych, wydajności procesów oraz zarządzania jakością, jak również planowania procesów są dostępne w czasie rzeczywistym i zoptymalizowane w zintegrowanej sieci. W aspekcie integracji pionowej oczekuje się powiązania zamówień od klientów zewnętrznych na folię z wykorzystaniem 50% regranulatu z możliwościami jego produkcji przy zmiennej ilości różnorodnych grup odpadów własnych.
Stąd automatyzacja umożliwia identyfikację, planowanie i śledzenie w czasie rzeczywistym powstawania odpadu własnego oraz możliwość jego recyklingu pod kątem przygotowania surowca (regranulatu) do produkcji nowych wyrobów z folii w obiegu zamkniętym.
Proces sterowania oparty jest o sygnały zdefiniowane i generowane przez urządzenia (z czujników PLC), rejestrowane i przetwarzane w chmurze obliczeniowej. Głównym generatorem sygnałów odnoszących się do przepływu materiałów są: prasa (wydajność, nacisk), automatyczny system transportowy, systemy buforowania materiałów.
Poprzez zsynchronizowanie parametrów zespołów i maszyn bazujących na stabilnej wydajności procesu produkcyjnego zapewnia się płynność przepływu surowców/materiałów, eliminując wąskie gardła, a zapewniając równomierny takt produkcji, bezpieczeństwo procesu w ujęciu zasobów ludzkich i technicznych.
Wybrane elementy linii wyposażono w elementy sterowania umożliwiające pomiar parametrów sterowania oraz ich modulacji w zakresie optymalizacji procesu produkcyjnego.
3. Optymalizacja automatycznej linii regranulacji
Podczas badań przeprowadzono pomiary wydajności recyklingu, którego miarą jest wydajność masowa wytwarzania regranulatu. Określono wpływ zmiennych parametrów technologicznych procesu (temperatury, ciśnienia, czasu) na przebieg procesu recyklingu, którego wskaźnikami będą oczekiwana wydajność i sprawność energetyczna. Dla otrzymanych przy różnych nastawach parametrów technologicznych poszczególnych grup regranulatu własnego (rodzaj tworzywa, kolor, udział powierzchni zadrukowanej) wykonano pomiary wskaźnika szybkości płynięcia oraz pomiary zawartości zanieczyszczeń. Następnie z odpowiedniego rodzaju regranulatu wykonano próbki folii, dla których przeprowadzono badania właściwości mechanicznych.
Badania wydajności recyklingu, w szczególności wydajności granulowania nie wymagają odrębnej specjalistycznej aparatury pomiarowej, bowiem w przeważającej mierze opierają się na odczycie i analizie nastaw parametrów technologicznych na poszczególnych urządzeniach tworzących linię do recyklingu oraz na pomiarach podstawowych wielkości fizycznych, takich jak masa surowca podawanego na linię do recyklingu, masa odfiltrowanych zanieczyszczeń czy masa otrzymanego regranulatu.
Proces badawczy obejmuje analizę wybranych parametrów mechanicznych i jakościowych produkcji regranulatu w ujęciu optymalizacji wydajności i równomierności procesu.
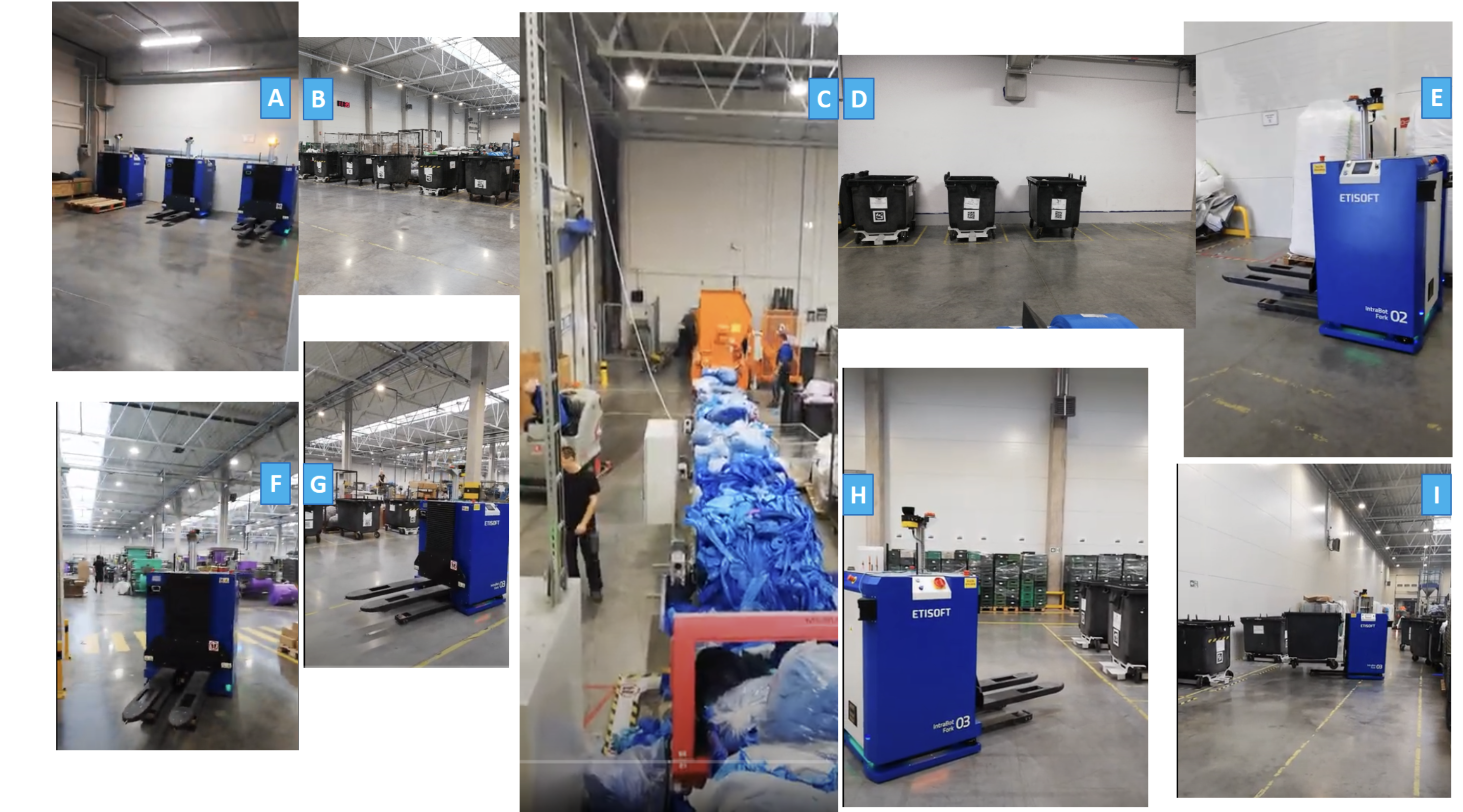
Rys. 9. Instalacja demonstratora automatycznej linii regranulacji: A-miejsce postoju i obsługi wózków AGV; B-Punkt odbioru odpadu na hali produkcyjnej; C-widok: praca, transporter i waga linii regranulacji oraz magazyn buforowy odpadu; D-punkt postoju koszy z odpadem przy magazynie buforowym regranulacji; E-robot AGV odbiera i odstawia „big-bag” z regranulatem do magazynu surowca POLIPAK; F,G,H-widok robota AGV; I-robot AGV odkłada kosz na miejscu buforowym.
Dane uzyskiwane w wyniku powyższych analiz będą w kolejnych warunkach eksploatacyjnych umożliwiały korektę nastaw parametrów mechanicznych pracy poszczególnych maszyn i urządzeń, celem poprawy przebiegu procesu produkcyjnego.
Oznacza to, że empirycznie wyznaczone optymalne zakresy parametrów pracy urządzeń i maszyn w procesie produkcyjnym, gwarantują uzyskanie założonych wielkości technologicznych (tj. wydajność produkcji około 550 kg/h) dla regranulatów z różnych grup odpadów, z jednoczesnym spełnieniem zdefiniowanych parametrów jakościowych, umożliwiających wprowadzenie ich do powtórnego przetwarzania w produkcji folii o grubości poniżej 30 μm (zgodnie z innowacją produktową).
4. Podsumowanie
1. Realizacja projektu wynikała z zapotrzebowania rynku na produkty branży tworzyw sztucznych, w której od lat z powodzeniem jest Polipak Sp. z o.o., który produkuje opakowania i worki na śmieci, spotykane na rynku m.in. pod marką „Jan Niezbędny”. Utrzymanie stabilnej pozycji na rynku opakowań wymaga posiadania najnowocześniejszych maszyn i urządzeń pozwalających na doskonalenie techniki i technologii produkcji. POLIPAK nieprzerwanie od lat dziewięćdziesiątych, z widoczną dużą intensyfikacją realizuje projekty inwestycyjne, których celem jest zwiększenie oferty produktowej, poprawienie jakości produktów, zwiększenie mocy i elastyczności produkcji, wzmocnienie pozycji na rynku, pozyskanie nowych klientów, dywersyfikacja branż odbiorców opakowań, zwiększenie sprzedaży wyrobów za granicę oraz ograniczenie oddziaływania na środowisko naturalne w procesie produkcji.
2. Nowy, wysoce innowacyjny w skali europejskiej proces produkcyjny pozwolił Spółce rozszerzyć ofertę produktową o produkty pochodzące z odzyskiwanych materiałów, umocnił pozycję na rynku, pozwolił zdobyć pozycję innowatora w branży, zwiększyć przychody ze sprzedaży, zachować zdolność do dalszego rozwoju. W wyniku realizacji projektu Polipak zwiększył zarówno zdolności produkcyjne, jak i techniczne i technologiczne. Wdrożenie wyników prac B+R pozwoliło uruchomić produkcję wyrobów spełniającą oczekiwania większości odbiorców, związane z ekologią i zrównoważonym gospodarowaniem zasobami.
Artykuł powstał w ramach realizacji
przez POLIPAK Sp. z o.o. projektu NCBR
nr: POIR.01.01.01-00-0783/19
dr inż. Paweł Zając, Politechnika Wrocławska,
mgr inż. Tomasz Tramś, Prezes, Polipak sp. z o. o.,
dr hab. inż. Waldemar Woźniak, prof. uczelni, Uniwersytet Zielonogórski,
dr hab. inż. Michał Sąsiadek prof. uczelni, Uniwersytet Zielonogórski,
dr inż. Maciej Niedziela, Uniwersytet Zielonogórski,