Oszczędności energii w procesie chłodzenia granulatu
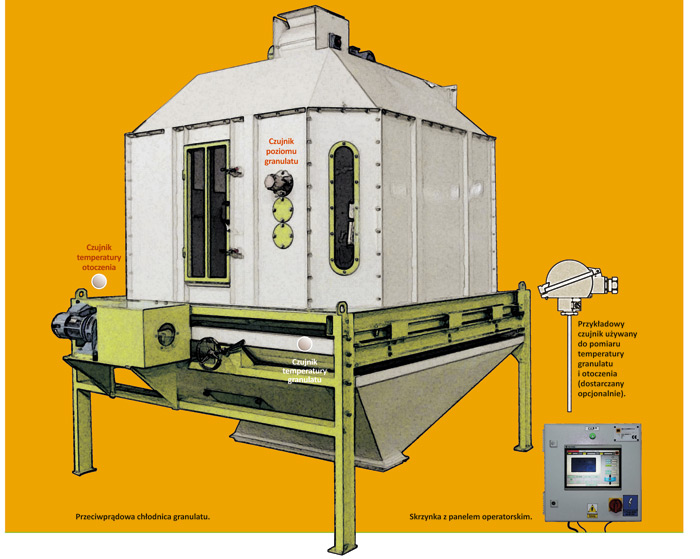
Proces produkcji granulatu (pelletu) odbywa się w granulatorach. Proces przeciskania „peletek” przez matrycę wytwarza znaczne ilości ciepła. Po wyjściu ich temperatura sięga 80°C. Z uwagi na właściwości mechaniczne oraz biologiczne granulka musi zostać schłodzona. Zazwyczaj jest to temperatura nieprzekraczająca 10° powyżej temperatury otoczenia. Odebranie znacznej ilości ciepła wymaga urządzenia zwanego chłodnicą, które – wyposażone w wentylator – pozwala na szybkie obniżenie temperatury granulek bez ograniczania wydajności granulatora. Moc stosowanych wentylatorów waha się od 20 do 60 kW w zależności od wielkości chłodnicy. Najczęściej są to chłodnice tzw. przeciwprądowe (ang. counterflow), które wykorzystują przepływ powietrza przez warstwę granulki w kierunku przeciwnym do przemieszczania się produktu.
Badania potwierdzają, że zużywana przez wentylatory energia nie jest optymalnie wykorzystywana. Wynika to ze skomplikowanej fizyki procesu chłodzenia, konstrukcji samych chłodnic oraz sposobu sterowania pracą chłodnicy. O ile na dwa pierwsze czynniki trudno mieć wpływ, o tyle ten ostatni pozostawia nam sporo możliwości.
Zysk ze sterowania
Większość chłodnic jest sterowana w bardzo prosty sposób: w momencie uzyskania odpowiedniego poziomu (stwierdzanego czujnikiem) ruszt spustowy chłodnicy otwiera się na ustalony czas. Powoduje to wysyp granulek znajdujących się na samym dnie, które są w tym momencie najchłodniejsze. Są one zastępowane przez granulat cieplejszy, który przesuwa się na ich miejsce. Warstwa granulatu z góry jest uzupełniana nowym produktem pochodzącym z granulatora.
Czujnik ustawia się na takiej wysokości, aby w każdych warunkach temperatura granulki była niższa od dopuszczalnej (dokładnie: aby różnica temperatur granulki i otoczenia nie przekraczała dopuszczalnej wartości), a jej wilgotność nie większa od dopuszczalnej normami.

Efekt przeciągania chłodnicy
Tego typu sterowanie zapewnia dopasowanie wydajności chłodnicy do wydajności granulatora. Jednak nie zapewnia optymalnego zużycia energii. Wynika to z faktu, że czas przebywania granulki (czas chłodzenia) w chłodnicy jest silnie uzależniony od jej wielkości, składu i wilgotności. Praktyka wygląda w ten sposób, że wysokość czujnika ustawia się tak, aby pasowała do wszystkich przypadków. Prędkość obrotowa wentylatora jest stała i niezależna od rodzaju granulatu. W efekcie większość chłodnic niepotrzebnie przechowuje granulki, które nie zmieniają już swojej temperatury, a pozostają w chłodnicy i powodują większy opór przepływającego powietrza, czyli de facto wentylatora (tzw. przeciągnięcie chłodnicy).
Zatem optymalne sterowanie to takie, w którym konkretna granulka osiąga swoją temperaturę dopuszczalną spustu dokładnie w momencie, kiedy czujnik poziomu zostaje wzbudzony. Ponadto chłodnicę opuszczą wszystkie granulki, których już nie można bardziej wychłodzić (likwidacja przeciągnięcia).
Sposób optymalizacji
Z uwagi na szereg czynników wpływających jednocześnie optymalizacja zużycia energii nie jest możliwa przez manualną zmianę prędkości falownika zasilającego wentylator.
Można to uzyskać przez odpowiednią regulację prędkości wentylatora w całym procesie chłodzenia, przy jednoczesnym pomiarze temperatury dolnej warstwy granulek oraz temperatury otoczenia: pierwszym zapełnianiu, pracy normalnej i czyszczeniu. Stworzenie optymalnego regulatora wymagało stworzenia i przetestowania modelu matematycznego zjawisk zachodzących w procesie chłodzenia na każdym jego etapie oraz skomplikowanej analizy poziomu ich wpływu na konsumpcję energii. Badania wykazały również, że przy tak uformowanym procesie sterowania oczekiwaną wilgotność granulki otrzymujemy niejako „przy okazji”, jako korzystny „efekt uboczny”.
W efekcie prac podjętych w ZA ZREMB WARSZAWA powstało urządzenie SmartCooler, które może pracować jako niezależne lub we współpracy z nadrzędnym systemem sterowania. Wyposażone jest w panel operatorski pozwalający na dokonanie wstępnej konfiguracji podczas wdrożenia oraz monitorowanie podstawowych parametrów: temperatury, czasu chłodzenia, zużycia energii. Oczywiście zakłada ono obecność falownika zasilającego wentylator.
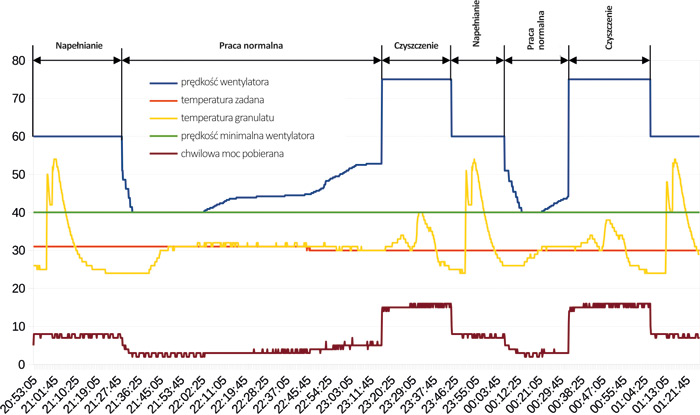
Przykładowy cykl pracy chłodnicy sterowanej przez SmartCooler
SmartCooler jest dostarczany w postaci skrzynki z panelem operatorskim, szybkim czujnikiem temperatury granulatu, czujnikiem temperatury otoczenia oraz dokumentacją. Zestaw umożliwia samodzielny montaż i uruchomienie przez służby utrzymania ruchu w zakładzie. Dostępna jest również usługa wdrożenia przez producenta.
Obecnie SmartCooler pracuje w około 20 liniach produkcyjnych. Wdrożenia potwierdziły oczekiwane oszczędności na poziomie od 40 do 70% energii zużywanej przez wentylator. Kalkulacja kosztów wskazuje, że przy wentylatorach dużych mocy (50 kW i więcej) koszt SmartCoolera zwraca się w ciągu 12–18 miesięcy. Przy rosnących cenach energii elektrycznej okres zwrotu może okazać się jeszcze krótszy. W przypadku wentylatorów małej mocy (20 kW) może być to okres dłuższy, uzależniony od faktycznego obciążenia wentylatora przy prędkości 50 Hz.
Analizie zostały poddane również procesy wstępnego załadunku (przy pustej chłodnicy) oraz czyszczenia (całkowite opróżnianie chłodnicy). Oznacza to, że SmartCooler również znacznie oszczędza energię przy krótkich seriach produkcyjnych.
Zastosowane algorytmy sprzyjają również utrzymaniu oczekiwanej wilgotności pelletu. Niemniej jednak są prowadzone obecnie prace nad wyposażeniem SmartCoolera w niezależny pomiar wilgotności.
Zakład Automatyki ZREMB Warszawa Sp. z o.o.
03-810 Warszawa, ul. Gocławska 11
tel. 22 810 22 96, 22 810 22 70
e-mail: biuro@zawzremb.pl
www.zawzremb.pl
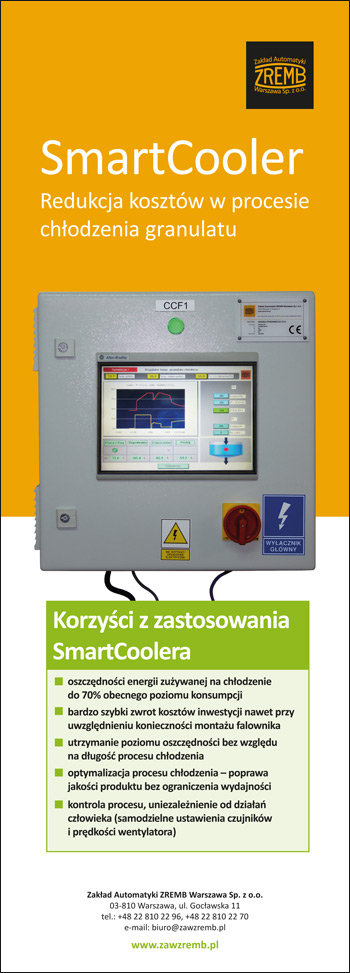