Przyspieszenie inteligentnej produkcji i wysoka precyzja – terminal IND360
8 kluczowych zasad automatyzacji systemu ważeniaPrzyspieszenie inteligentnej produkcji i wysoka precyzja – terminal IND360
Kontrola na podstawie masy to doskonały wybór dla konstruktorów maszyn i integratorów systemów, ponieważ zapewnia większą produktywność i spójność w porównaniu z innymi metodami kontroli. Ponadto czujniki masy lub wagi nie mają fizycznego kontaktu z mierzonymi produktami. Zmniejsza to wymagania dotyczące czyszczenia i zapobiega zanieczyszczeniom krzyżowym. Mimo że metoda ta może być stosowana w przypadku procesów mierzonych w ciągu minut lub godzin, oferuje ona również znaczące korzyści dla systemów o wysokiej wydajności produkcyjnej, w których pomiary są wykonywane w ciągu kilku sekund lub krócej. Oto osiem aspektów idealnej automatycznej kontroli opartej na masie, które należy wziąć pod uwagę podczas tworzenia maszyn działających w dowolnym punkcie łańcucha pomiarowego automatyzacji.
1. Łączność z przemysłowymi sieciami Ethernet
Najlepszym rozwiązaniem jest inteligentny system automatycznego ważenia, który obsługuje wiele standardów IE i jest wystarczająco elastyczny, aby łączyć się z różnymi sieciami IE. Zastosowanie terminala, takiego jak METTLER TOLEDO IND360,
zapewnia tę elastyczność, umożliwiając jednocześnie niezawodną standaryzację funkcji łączności i sterowania.
2. Komunikacja typu „podłącz i waż"
Inteligentny, przyszłościowy system automatycznego ważenia powinien umożliwiać komunikację zarówno z technologią operacyjną (OT), jak i z sieciami informatycznymi (IT) oraz usługami w chmurze. Korzystając z tego samego programu ze sterownikiem PLC lub rozproszonym systemem sterowania (DCS), SAI umożliwia użytkownikom podłączenie wag tensometrycznych i inteligentnych urządzeń METTLER TOLEDO, jak precyzyjne wagi stołowe, wagi podłogowe i moduły wagowe, które ułatwiają zintegrowane ważenie w zakresie od 11 gramów do 1000 ton. SAI obsługuje również monitorowanie stanu i alarmy Smart5™, które automatycznie powiadamiają system automatyki, gdy czujnik lub waga nie mogą przesyłać dokładnych danych ważenia.
3. Raportowanie zdarzeń i alarmów
Liczba informacji o stanie zainstalowanych czujników i systemów może przytłaczać operatorów w Twoich obiektach, utrudniając im szybkie reagowanie w przypadku awarii lub nadchodzącego problemu. Protokół SAI przekazuje status alarmu Smart5 do sterownika PLC lub rozproszonego systemu sterowania (DCS) w czasie rzeczywistym, a terminal IND360 zapewnia konkretne wskazówki dla operatorów w przypadku wystąpienia problemu, dzięki czemu mogą oni szybko wyeliminować jego przyczynę. Dzięki temu zyskujesz pewność, że wszelkie nieoczekiwane problemy zostaną szybko zgłoszone w celu uzyskania natychmiastowej reakcji lub przeprowadzenia zaplanowanej konserwacji, w zależności od priorytetu alarmu.
4. Funkcje zgodności
Twoje urządzenia wagowe powinny spełniać zarówno międzynarodowe, jak i lokalne standardy zgodności. Każdy kraj może wymagać specjalnych certyfikatów zgodności z przepisami, dlatego ważne jest, aby skonsultować się z dostawcą przed określeniem systemu. Inne certyfikaty związane ze zgodnością obejmują te dotyczące stref niebezpiecznych, takich jak ATEX, IECEx lub FM, oraz standardy łączności, w tym Profibus International (Pl), Open Device Vendors Association (ODVA) i EtherCAT Technology Group (ETG). METTLER TOLEDO spełnia te globalne standardy zgodności z przepisami i dysponuje rozległą siecią personelu na całym świecie, aby zapewnić, że Twój sprzęt zostanie zainstalowany zgodnie z nimi, umożliwiając szybkie i bezproblemowe uruchomienie.
5. Integracja systemu sterowania
Zastosowanie certyfikowanego interfejsu automatyki jednej z powyższych organizacji pozwala zaoszczędzić cenne godziny pracy inżynierów, testowania i rozwiązywania problemów z uruchamianiem. Aby jeszcze bardziej uprościć integrację, METTLER TOLEDO dostarcza przykładowy kod programowania, który pozwala lepiej zrozumieć podstawowe dane urządzenia i funkcje sterowania. Dostępny jest przykładowy kod programowania dla systemów sterowania Rockwell i Siemens.
6. Inteligentniejszy terminal
Konstruktorzy maszyn i integratorzy systemów sterowania zwykle poświęcają mnóstwo czasu i wysiłku na programowanie sterowników PLC, aby stworzyć w pełni funkcjonalny i skuteczny system ważenia w ramach kontroli procesu. Wbudowany interfejs internetowy zapewnia lepszą wizualizację procesu, co ułatwia konfigurację i konserwację. W rezultacie system napełniania działa szybciej, a wielu klientów może zastąpić podawanie z dwiema prędkościami podawaniem z jedną prędkością dzięki szybkości działania wbudowanej aplikacji. Ta zmiana upraszcza konstrukcję maszyny i pozwala znacznie ograniczyć koszty. Te wstępnie zaprogramowane aplikacje prowadzą do poprawy wydajności procesów, a jednocześnie standaryzacji konserwacji za pomocą jednego terminala automatyki.
7. Wyjątkowa szybkość i precyzja
Zastanów się, ile czasu potrzebuje Twoje urządzenie lub system, aby zareagować na zmianę wagi. Jeśli jesteś projektantem, który oczekuje wysokiej wydajności i szybkości, urządzenia o ultraszybkiej częstotliwości aktualizacji mogą zapewnić najwyższą dokładność i powtarzalność w najkrótszym czasie, dzięki czemu system sterowania może podejmować precyzyjne decyzje we właściwym momencie. Oznacza to, że urządzenie ważące musi nie tylko szybko obliczać masę, ale także być w stanie udostępniać dane zarówno wbudowanym aplikacjom, jak i sieci automatyki z bardzo dużą częstotliwością.
8. Wydajność i łatwość serwisowania
Po zainstalowaniu terminala z czujnikiem tensometrycznym lub „inteligentną" wagą należy udokumentować parametry konfiguracji i wartości adiustacji (kalibracji). Najłatwiej można to zrobić za pomocą interfejsu internetowego, który umożliwia tworzenie kopii zapasowych urządzenia na komputerze lub serwerze. Jeśli urządzenie ważące ulegnie uszkodzeniu, wartości konfiguracji i adiustacji można łatwo przywrócić do nowej jednostki, eliminując długi czas przestoju, który zwykle wymaga konfiguracji i pełnego cyklu wzorcowania/adiustacji. O ile sama waga nie jest uszkodzona, wartości adiustacji z początkowej instalacji zwykle wystarczają do przywrócenia sprawności. Jeśli jednak zostanie zauważona różnica między wartościami adiustacji początkowej i przywróconymi, może to oznaczać, że nagromadzony materiał przesunął wartość zerową lub nadal znajduje się w wadze lub na niej. Oczywiście najlepszą praktyką jest dodanie znacznej liczby odważników wzorcowych w celu sprawdzenia poprawności działania przed włączeniem systemu, aby potwierdzić, że waga nadaje się do użytku. Podczas pracy ważne jest również, aby rutynowo testować wagę w celu zapewnienia prawidłowego działania i potwierdzenia, że żadne nieprzewidziane zdarzenia nie wpłynęły negatywnie na jej dokładność. Liczba i rodzaj przeprowadzanych rutynowych testów zależy od wagi, krytyczności procesu oraz znaczenia dokładności ważenia w punkcie, w którym waga jest zintegrowana. Rutynowe testy potwierdzają, że żadne wyjątkowe zdarzenia nie wpłynęły negatywnie na dokładność wagi. Niektórzy twierdzą, że standardy miar i wag określają rutynowe cykle testowania, jednak korzystanie z tego rodzaju porad nie pomoże zapewnić bieżącej dokładności i jakości. Zalecenia lub weryfikacja w ramach programu Good Weighing Practice (GWP®) firmy METTLER TOLEDO to lepszy wybór, ponieważ na podstawie tolerancji procesu i ryzyka pozwala określić, jak często należy wykonywać testy.
www.mt.com
www.mt.com/IND360
www.mt.com/IND360
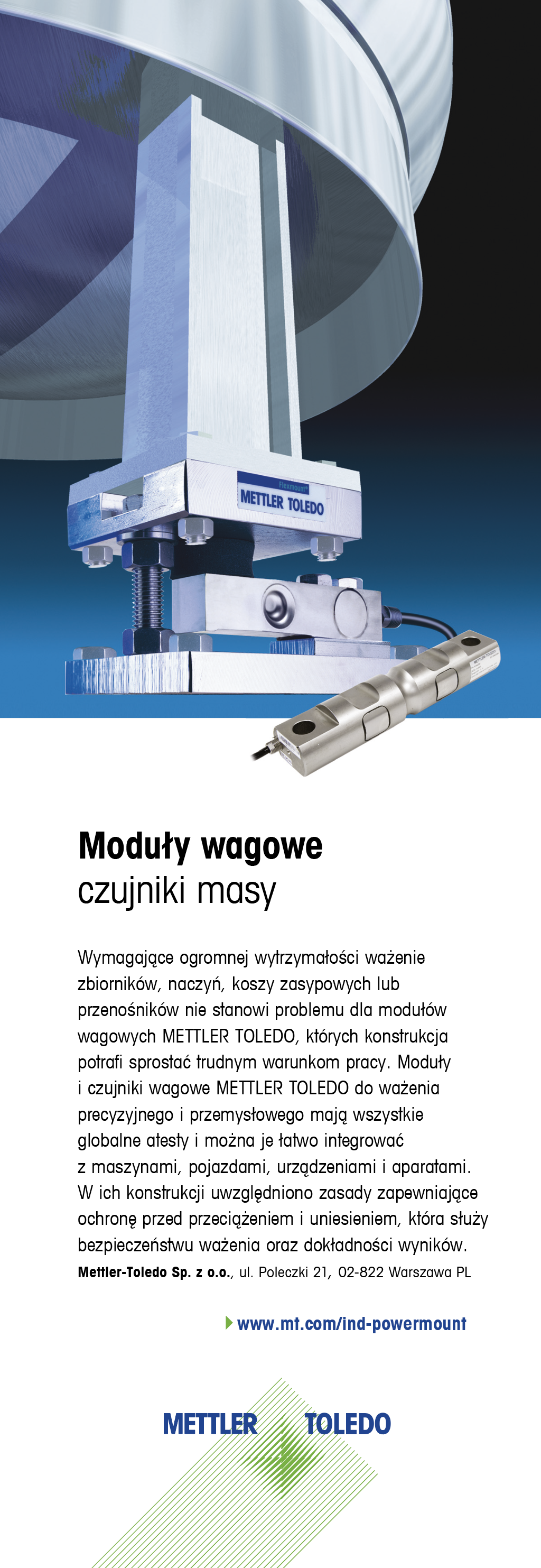